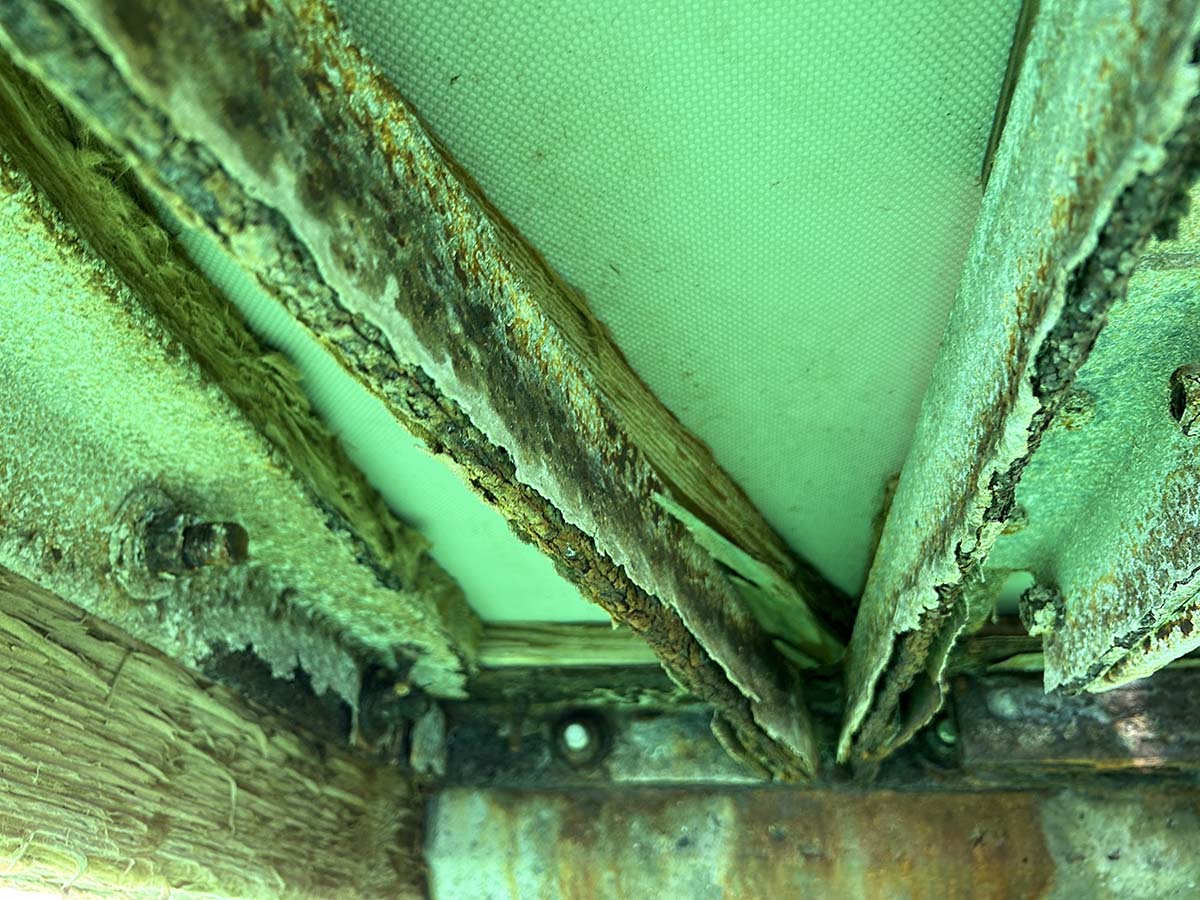
The Challenges of Existing Structures
Published on April 28, 2025During a college engineering course, my professor proposed a question to the students. “You construct a flawless theory—airtight reasoning, clean premises, a clear and necessary conclusion. You test it through modeling. You gather data. The results don’t match the prediction. What is wrong: the theory, or the model?”
The class was still for a moment, each student absorbing the professor’s questions. Half of my classmates were graduate students in the department of economics. The other half, engineering students like me, were in the class as a necessary elective. As the conversation unfolded, almost all economists and engineers alike landed on the same answer: if the numbers didn’t calculate out, of course your theory is wrong.
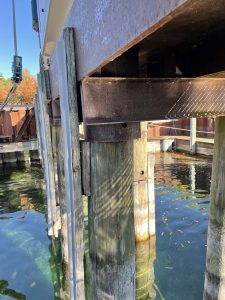
However, the professor kept provoking—that answer did not really satisfy his expectations. As he approached me, I continued to mull this over. As my mind raced to finalize my smattering of thoughts into a coherent answer, I heard myself mutter: “The model is wrong, not the theory.” The professor smiled and walked back to the front of the class. He’d finally gotten the answer he was fishing for.
As economist and Nobel Laureate F.A. Hayek observed, even the most precise models are only as reliable as the assumptions that they’re built on. If those assumptions do not reflect the true nature of the system, then no amount of mathematical refinement will make the outcome meaningful. Hayek wrote, “The real difficulty, to the solution of which science has little to contribute, and which is sometimes indeed insoluble, consists in the ascertainment of the particular facts.”
Engineering and Marina Design
This lesson applies to engineering just as much as it applies to economics. The more time I spend working with complex models, the more I’ve come to appreciate the old maxim: “Garbage in equals garbage out.” Results are only as reliable as the assumptions we make and the data we input. And yet, in marina engineering, we are often expected to offer precise answers to inherently imprecise questions: How resilient will a floating dock be under future storm conditions? What is the expected rate of overtopping on a breakwater? How many years remain in the life of a deteriorating pier?
This issue is especially pressing, given the current state of marina infrastructure in the United States. While there are notable exceptions, most marinas were constructed in the 1970s or 1980s. Meanwhile, vessel characteristics have increased—not only in length, beam and profile height, but also with unconventional elements such as swim platforms, outriggers and specialized power requirements. The industry is now challenged to accommodate these larger demands with aging infrastructure; therefore, topics such as engineering assessments, maintenance and rehabilitation strategies and structural retrofitting have become a focal point.
Accordingly, many requests for engineering proposals include language such as, “Conduct a field investigation, and provide a structural assessment. Then, estimate the remaining service life of the structure.” In response, we’ve provided statements along the lines of: “Considering all observed conditions, we assess the existing timber pier to be in fair condition. Given that the structure is approximately 25 years old, we estimate a remaining service life of up to 25 years.”
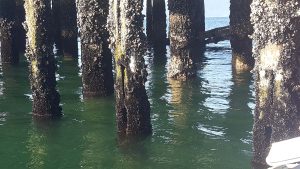
However, some clients interpret such statements as, “No maintenance or action is required for the next 25 years. This is what the engineers have concluded.” Understandably, such interpretations often lead to further discussion. Clients are sometimes surprised to learn that a service life estimate is not a fixed timeline; rather, it’s an informed judgment instead of a guarantee. It reflects what we’ve observed, what we know from precedent and what current engineering standards suggest. But it must always be understood in context: assumptions matter, and existing structures carry uncertainties.
Valuing Inspections
To illustrate how such assessments are formed, and where the nuance lies, it’s helpful to walk through a representative example. The following observations, inspired by actual assessments conducted in the past, demonstrate how various visible conditions, construction details and contextual factors together formulate a logical conclusion.
During a structural inspection, a steel cross beam supporting a pier’s timber superstructure is observed to have noticeable surface rust and measurable loss of material. The engineering team uses a wire brush to remove surface corrosion and measures a flange thickness of 0.421 inches. Despite the observable deterioration, the team does not notice any visible evidence of bending, warping or any permanent deformation of the beam’s original shape.
Back at the office, the team reviews inspection photographs and compares them to the client’s record drawings, which include the original as-built conditions. These drawings indicate that the beams were originally specified as W12x40 steel sections, with flange thicknesses of 0.515 inches. The measured thickness shows a material loss of just over 18%.
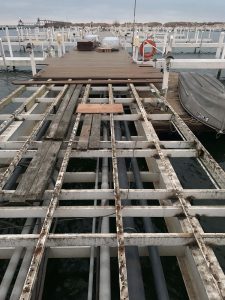
Referring to Waterfront Facilities Inspection and Assessment published by the American Society of Civil Engineers, the engineers assign a damage rating to each structural element observed. The guidance classifies damage ranging from “no defects” to “severe.” The observed conditions fall within the “moderate” range.
Knowing the approximate installation date, the team calculates an annualized corrosion rate based on the observed flange thicknesses. The current section remains structurally adequate and meets all relevant code requirements despite the observed reduction in material. Using this information, team members estimate that, assuming a consistent corrosion rate, the beam could continue to perform for another 15 years before the estimated loading demands exceed its remaining capacity. This estimate is further supported by historical precedent. Steel sheet pile walls in a similar location within the marina basin required replacement after approximately 40 years, closely aligning with the projected service life of the beam in question.
No matter how elegant this conclusion seems, the team also recognizes that this analysis is built on several assumptions. What if lake levels rise, exposing the beam to increased splash and accelerated corrosion? What if larger-than-normal vessels are berthed nearby, or if the region experiences stronger storms during peak boating seasons? Acknowledging the limits of any model to account for all possible future conditions, the team includes the following recommendation: “Further engineering investigations, similar to the one performed for this report, should occur every five years and after any significant storm events. This interval may be adjusted based on findings in future assessments.”
Even the most precise model is only as reliable as the assumptions that it’s built on. Those assumptions are too numerous to quantify, but they follow from practical experience. They span broad areas of knowledge—from loading expectations, design intent, material properties and evolving boating trends. The math may be flawless, but if these foundational assumptions are off, the results can be misleading. This is why sound engineering insight, rooted in precedent, design experience and real-world understanding, is essential to providing useful recommendations.
Practical Observation
While engineers must consider much more than pure physics and mathematics, it should not be construed as suggesting that engineering models are not valuable. On the contrary, these tools remain essential, but their application must be tempered by practical observation, precedent and established standards of practice. When a marina owner receives an engineering assessment, he or she is not simply receiving a calculation. He or she is receiving a professional insight. It is a tool meant to aid in prioritization, budgeting and repair. It is not a crystal ball. It is a professional opinion, shaped by the rigor of engineering methods and grounded in centuries of accumulated practical knowledge within the civil engineering profession.
While it may never be as “precise” as a lab test or a clean mathematical expression, it is forged in the same discipline, tested through experience and informed by countless real-world examples.
In complex and uncertain environments like marina infrastructure, this kind of engineering judgment is not a fallback. It is the foundation for sound decision-making. It is a springboard for advancing practical improvements, responsible investments and long-term structural resilience.
Nick Cortes, EIT is an engineer at Edgewater Resources. He can be reached at ncortes@edgewaterresources.com
Categories | |
Tags |