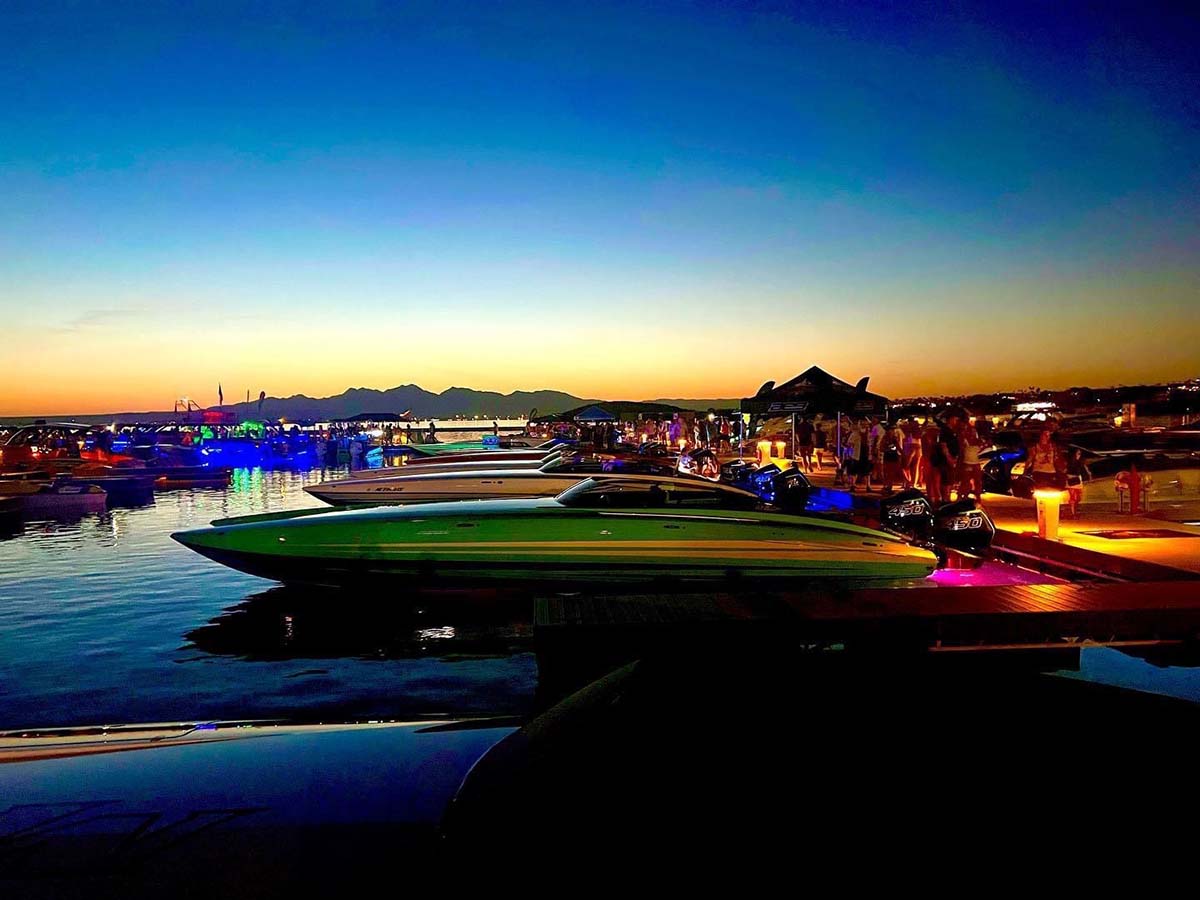
Creating a Desert Oasis
Published on August 15, 2023Arizona may often be overlooked as a boating state, but despite the vast desert area, the state also has areas of prime boating. Lake Havasu City is one such area, boasting 60 miles of uninterrupted navigable waterways complete with lake coves and 400 miles of river coastline. Water access recently increased substantially with the completion of phase 1 of the Havasu Riviera Marina, a concession of Lake Havasu State Park, and a piece of the larger Riviera Lake Havasu development.
The full project, when complete, will transform 550 acres of lakeside desert land into an entirely new residential development and public marina. The property will have close to 600 homes, 280 acres of recreational and educational areas to be developed by Lake Havasu City, and a state-of-the-art marina. The land transformation stems from a partnership between Lake Havasu City, Arizona State Parks and Trails, Komick Enterprises, and Desert Land Group.
The lead engineer for the marina was Christopher Goshow, P.E., principal at International Waterfront Consultants (IWC), who worked alongside his team from early analysis to construction. The groundbreaking for the facility occurred in 2019 and a soft opening was held on Labor Day 2022. This past spring marked the start of the marina’s first full boating season.
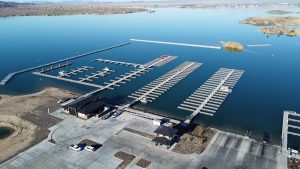
Innovative Engineering
As with any marina development, the project began with a series of studies and analyses to determine exactly what the site could accommodate.
A wind/wave study was conducted to determine the impacts from an average summer storm up to a 100-year event. The objective of the study was to structure the marina to withstand the worst-case scenario. This was combined with a berth tranquility study that examined the target conditions in a berth for a boat to withstand common or once-in-a-100-year events. “Let’s say our study shows waves will be 2 feet in a one-year storm, and 4 feet in a 50-year storm, but I need waves of half that size to keep the boats and docks safe. That means I need a wave attenuator that can knock down waves by half,” Goshow explained. It’s then his job to calculate the draft, dock width, and anchor load for the attenuator that can subdue the impacts from the wave and wind action.
While these studies and the use of attenuators are common practices, what Goshow did differently in this project was the anchoring. The IWC team developed a conceptual design of a floating wave attenuator that was double-skirted with floating panels, and held in place with helical screws with a load testing of up to 50,000 lbs. He chose helical screws and synthetic rope to keep the attenuator in place no matter what the winds and waves did. “There are marinas that just throw out anchor blocks with little engineering to support it and they find the blocks shift during a good storm. We do a lot of load testing to prevent that from happening,” he said.
The helical screws go into the seabed about 19 feet and are attached to a steel rod and then to a line. Goshow explained that anchors are driven straight and with the attenuator flush to the surface, wind and wave action pulls the anchors at an angle causing the steel rod of the anchor to bend. “The steel at the top will bend and be permanently deformed, but we realized that an equilibrium will be reached between scope and bend, where the rod will bend initially but it will never go past that point and rupture. That became the design anchor. We’d thought about putting the anchor in sideways to alleviate the bend but that would have been more challenging and expensive to install and likely wouldn’t have held as well,” Goshow said.
Similar ingenuity was used in choosing a synthetic rope, but the decision was easy. Goshow found the ¾ inch rope that he needed for the attenuator had a breaking point of 65,000 lbs. in the synthetic option, but just 21,000 lbs. in a double-braid nylon. “You’d need an inch and a half, about double to meet the same strength,” he said. This unique anchoring system was carried to the docks as well that used small helical screw anchors with synthetic rope moorings but for the docks, winches were utilized. The synthetic rope used is the latest iteration of ropes that uses better technology to increase the strength and size while minimizing the cost.
Houseboats
Phase 1 of the project is complete and includes about 280 slips. To meet demand, Phase 2 began in December 2022. Goshow said the interest in the marina has been much higher than anyone expected with parking lots filled and long lines for the boat ramp, and a waiting list for slips that are yet to be built. To try to meet demand, two steel fabrication plants have been running simultaneously to meet the permit deadline and get the project completed as fast as possible.
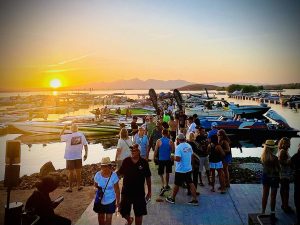
Phase 2 will add approximately 260 more slips, some of which may be covered. But unique to this phase is the addition of fully customized docks that will house luxury houseboats, known as the Havasu Yachts. Sold as fractional ownership properties, the structures are fully functioning boats ranging in size from 4 to 8 bedrooms that can accommodate between 8 and 18 people. Each comes with an adjoining 45-foot slip for owners to keep their boats, a 6-seater golf car with on-site parking, two kayaks, and two stand-up paddleboards.
The houseboats have fresh water piped in and grey water piped out through sewer lines that are plumbed right through the dock. Power for the boats comes through direct lines from the city’s power grid. Units are available in 6, 10, and 16 co-owned partnerships with 35-year licensing agreements. Along with the purchase price, partners also pay an annual fee for the lease of the slip, insurance, and maintenance. In addition, a cleaning fee is assessed after each use. The marina curates the partners who own the houseboat and accessories. Owners are allotted a set amount of usage of the penthouse each year dependent on the number of partners. A Zoom meeting is held annually to set up a calendar, although partners can trade and reserve time as needed.
Goshow said the penthouses were the brainchild of the owner who had seen a similar design in his travels and felt it would be a profitable addition to the Riviera project. With the houseboats nearly sold before they are constructed, his bet has paid off.
With the popularity of the area growing, once phase 2 is complete, the work may continue. There is a tentative Phase 3, but for now, Goshow said “Those plans are staying secret.”
Categories | |
Tags |