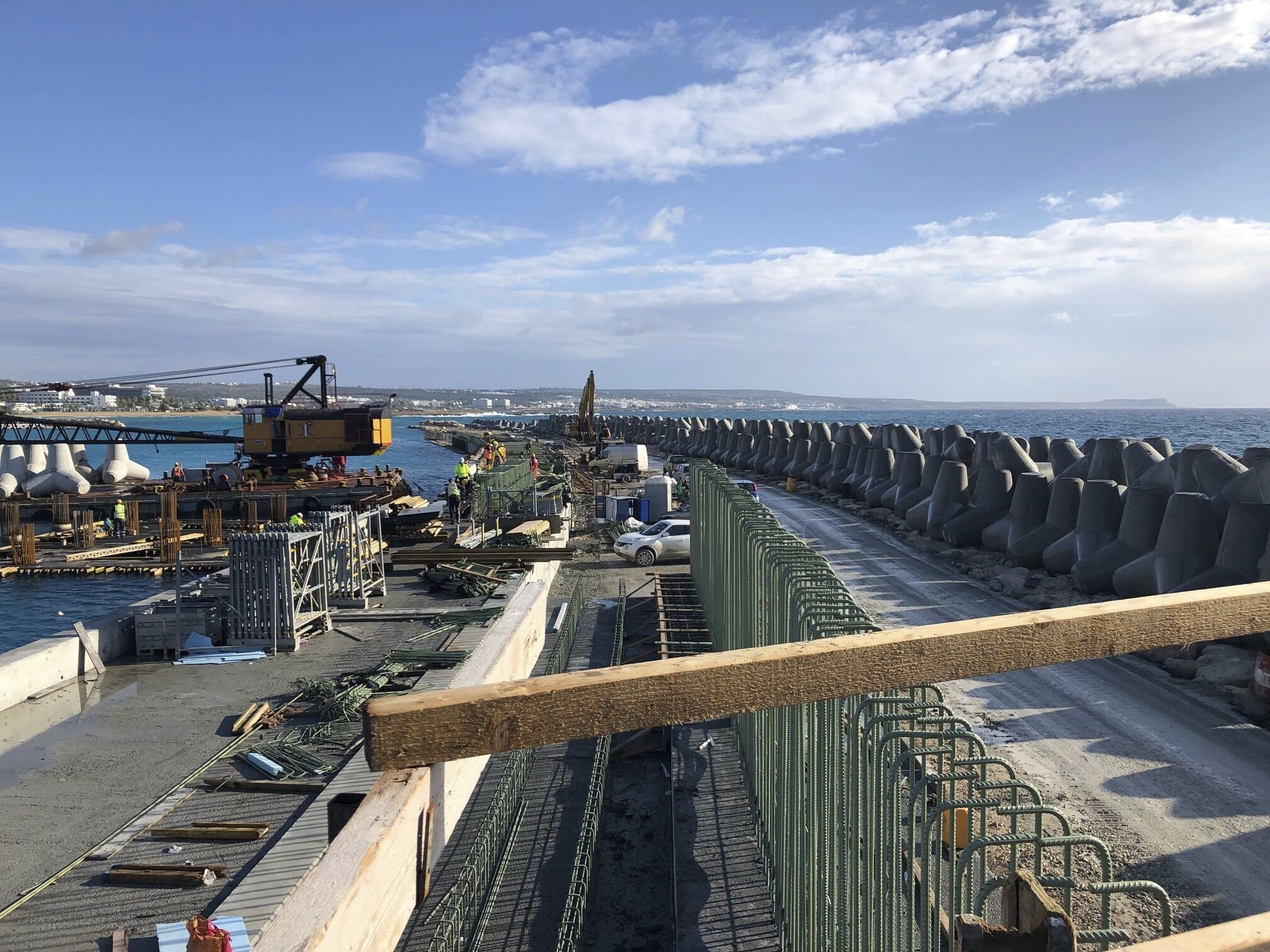
Future Proofing for Marinas: A Conversation on Contingency Planning and Risk Management
Published on May 1, 2020Two recent Water Marks articles on water level changes in the Great Lakes (MDA January/February and March 2020) highlighted the value of preparing to be wrong when planning for a new or rehabbed marina facility. For an industry with a long and storied historical memory of the most threatening conditions that boaters have faced on the water, preparing for unprecedented scenarios requires a new kind of mindset.
This shift in perspective and assumptions is especially important for marine and coastal engineers, who draw on an extensive range of historical data and accepted design approaches that have weathered the test of time. However, as new issues and challenges continue to arise (especially in relation to climate change), reliance on past standards and guidelines can potentially expose marinas to unexamined levels of risk. How can marina owners/operators and engineers best work together to address and manage the more dynamic and uncertain conditions their facilities are likely to face in the years ahead?
SmithGroup engineers Margaret Boshek and Robert Wright discussed some of the challenges and opportunities they are seeing for marina risk management. Their conversation highlights the value of exploring difficult questions early in the design process and clarifying the level of acceptable risk for a marina project.
Robert Wright (RW): Engineers pride ourselves on meeting our client’s budget. If you tell an engineer “I have $X to do this,” we will work extremely hard to find the best solution for that budget. But one of the problems with designing to a budget is that it can potentially increase your risk exposure.
Margaret Boshek (MB): The basis of design directly affects risk management – so it’s crucial to discuss that upfront. What conditions are we designing for? Given that x or y is likely to occur over the life of your facility, how risk adverse are you as a marina owner? Are you willing to spend more than your stated budget in order to manage those risks or would you prefer to set aside money for future repairs?
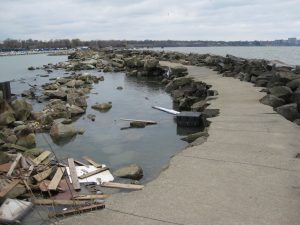
RW: I think in the past that baseline level of risk tolerance tended to be assumed rather than confirmed as part of a collaborative process with the client. Perhaps because it aligned with regulatory compliance standards. So engineers would design for the 100-year storm or wave event with the assumption that everyone understood what that was, and that it met the project requirements. But more and more we’re seeing that terminology gets in the way of understanding what the risks actually are – and how they’re
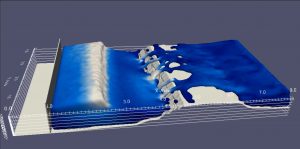
changing. Today’s minimum regulatory standards might not adequately protect your facility 10 years from now, or 20 years from now.
Terminology
MB: It’s easy to misinterpret what a 100-year storm is. People often think it’s a storm that statistically happens once every 100 years, when it actually has a 1 percent chance of happening in any given year. Meaning if that event were to happen this year, it still has a 1 percent
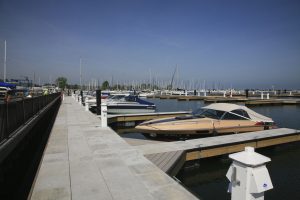
probability of occurring next year. But this is not what a “100-year return period event” suggests, so terminology like this is confusing and frequently misunderstood.
The Federal Emergency Management Agency (FEMA) and other organizations have moved away from using this terminology and instead talk about annual probability – the 1 percent storm. But it’s also important to recognize that probability compounds over time. For example, a 1 percent annual probability event has a 26 percent probability of occurrence over the next 30 years. As an owner, you might be willing to accept a 1 percent annual risk of catastrophic failure, but are you willing to take on that risk if it’s a 1 out of 4 chance over the next 25 years? It’s the same level of risk – but it doesn’t sound the same at all.
RW: This also relates to our reliance on hindcasting to determine what a facility’s risks are. Engineers are trained to think that the best way to predict and prepare for the future is by looking to the past. Our records of past wind, wave and weather conditions are viewed as the best indication of what future conditions are most likely to be for that location.
While this provides a level of comfort when designing for known extreme conditions today, it does not account for future extremes that are likely to change due to environmental factors. The climate trends we’re seeing, including warmer air and water temperatures, reduced ice cover, stronger storms, and changing sea levels, all need to be considered as part of forecasting a marina’s future conditions and operational needs.
Predicting Future Extremes
MB: The old engineering practice of solely looking to the past and applying rules of thumb needs to shift to a new way of thinking about construction and operations along the waterfront. At the same time, we know that some people are much more comfortable with hindcasting than forecasting. It’s easier to view past extremes as something that needs to be accounted for. Predicting future extremes is far less certain. Coastal and marine infrastructure are expensive, so no one wants to overpay for contingencies that might not be needed.
RW: The American Society of Civil Engineers offers great guidance for climate adaptive design. One of their recommendations is to design for “reasonable future extremes.” This sounds like an oxymoron, but it’s really another way of saying “Don’t try to eliminate all future risk from a project because you can’t.” You probably can’t afford it, for one thing.
MB: Yes, we’re seeing that dynamic now with some of the updated municipal and state guidelines for coastal protection. Some of the guidelines are based on very conservative assumptions – recommendations for the size of stone that should be used, for example. It takes all the risk out of that design decision – as well as all the engineering – but in many cases it’s overkill and a poor use of budget.
Managing risk doesn’t necessarily mean building more and paying more for it. We’ve found that a lot of money can potentially be saved by adjusting overly conservative design parameters to a higher but still acceptable level of risk. We can use numeric and physical modeling to test and verify the use of smaller stone than the guidelines recommend, for example. In other cases, we might see an engineer take an old breakwater cross-section and scale it up 20 percent to account for higher anticipated waves, assuming it will perform 20 percent better than it did before. But wave energy to increasing wave height is not linear and depending on the materials that are used and how it’s constructed, it might be more prone to failure at that size. It might also be larger than it needs to be. You need to test your assumptions and model them to verify the solution.
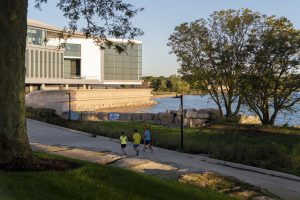
Modeling
RW: The modeling tools and software we use are extremely helpful for evaluating how a design alternative is likely to perform under different conditions. We analyze a range of scenarios, and it helps set guideposts for the final design. The key part of preparing to be wrong is to question your assumptions – so you avoid overreacting as well as underpreparing. Models give you a perfect way to do that – you can run multiple trials based on different assumptions.
We’re also able to verify our models with field data – and to calibrate them if we see differences. Nobody ever wants this to happen, but we had major flood and storm events hit during the construction of projects in Clarksville, Tennessee, and the nation of Cyprus. In both cases, we were able to verify our modeling assumptions. In Clarksville, city staff went out in a boat and measured floodwater depths and found them to be within three to six inches of what the models predicted for various parts of the site. All the critical systems and infrastructure were safely elevated above those levels.
MB: In the case of Ayia Napa Marina in Cyprus, we also encountered some seabed issues during initial construction that made excavation of the toe trench for the breakwater more difficult and costly. We went back to the lab to model possible modifications to the design, using wave gauge data that we had collected at the site to verify our original modeling assumptions. We were able to expedite redesign of the breakwater cross-section without compromising its structural resilience and reduce construction costs by $3 million Euros.
RW: That’s a great example of why risk management should continue through construction for complex coastal projects. Contractors are under a lot of pressure to keep a project on time and on budget – especially if they got the job by being the low bid. So ongoing review and input from the design engineering side during construction is a great way for owners to protect their investment. You need to expedite the right cost-saving or time-saving adjustments in the field to minimize your risk of paying much more for those changes later on.
MB: It’s tough to retrofit resilience. If you wait until after you need more protection or more flexibility, it’s too late. But it’s not an easy conversation to have with clients. When designing a new marina or refurbishing an older one, we like to focus on what will make that facility unique, appealing and profitable. No one likes to talk about under what conditions the proposed design might fail, and yet those discussions are precisely where the development of resiliency takes place.
For example, we frequently see owners conflicted about how tall a coastal protection structure needs to be to protect them from severe events versus the extent to which that structure impedes waterfront views. In terms of everyday operating conditions, the lower-profile structure has more short-term value to the owner, since it’s both less costly to build and makes the marina more attractive by increasing views to the water. So an owner can choose to accept more risk and go with a lower-profile structure, knowing that if water levels go up or a more severe storm hits, the protective capacity won’t be there.
RW: Every design decision carries some measure of risk, so a cost-benefit analysis is a great way to evaluate how best to manage it. The damages stemming from unmitigated risk can be calculated as dollar amounts in terms of repair, replacement, and how long it takes to get back up and running following a disruptive event. The analysis might show that anticipated failure under certain extreme conditions makes more financial sense than complete elimination of that risk. Since even small adjustments to a design can help reduce risk or increase resiliency, it’s best to weigh those adjustments from a cost/benefit rather than a straight cost standpoint. It leads to more informed design decisions.
Uncontrollable Risk
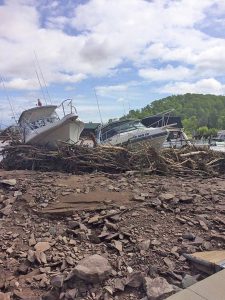
MB: One difficulty we’re seeing more of is risks related to infrastructure the marina owners can’t control. For example, many of Chicago’s municipal harbors are protected by federal breakwaters that are currently being overtopped due to high lake levels. Harbor managers can communicate the increased level of risk they’re seeing to their customers and constituents, but they are dependent on the U.S. Army Corps of Engineers for any repair or improvements to those breakwaters.
RW: Saxon Harbor in Lake Superior was destroyed by landside flooding that was triggered during an extreme precipitation event. Statistically these kinds of cloudburst events are becoming more frequent, so they represent a growing risk for marinas in certain locations. But landside flooding is not a risk that most marina owners have had to think about before – and there typically isn’t much a marina owner can do to mitigate its causes or impacts. If a key access road to your facility starts getting cut off by flooding on a regular basis, it could be completely outside your control to fix that.
MB: This is where the importance of insurance comes in. It’s important to know you’re fully covered for the damages you could suffer from extreme events – and that you’ll be able to rebuild in a way that will protect you better in the future. Some policies only cover the costs for rebuilding a facility in-kind and in place. In states where updated building codes and regulations require older facilities to upgrade with new materials or features when they rebuild, that kind of insurance policy will likely require the owner to pay the cost difference for the upgrades out of pocket. In the case of Saxon Harbor, its FEMA flood insurance would not cover the costs required to make the facility more resilient for future landside flood events.
Adaptability
RW: For locations facing larger variability in future operating conditions, adaptability will be key. Flexibility in design must become more of the norm for waterfront engineering. We’re seeing this at the regulatory level right now in the Great Lakes. Historically, you couldn’t get a permit for temporary coastal structures, but state agencies are relaxing that limitation to allow for faster and more cost-effective responses to the rapid rise in lake levels. This will be a huge help to coastal property owners, helping them get through a period of high water that is not going to last indefinitely.
MB: Building contingency measures into a design can make it easier to modify or adapt later if conditions change. Think of them as insurance or mitigation against larger repair or upgrade bills in the future. It all comes back to how having a clear understanding of the risk implications of design decisions allows the engineer and the owner to make more informed decisions that can have significant cost-saving implications when it comes to future-proofing a facility. Being able to design for risk, as well as aesthetics and profitability, is the best path toward a more successful, sustainable and resilient marina.
Categories | |
Tags |