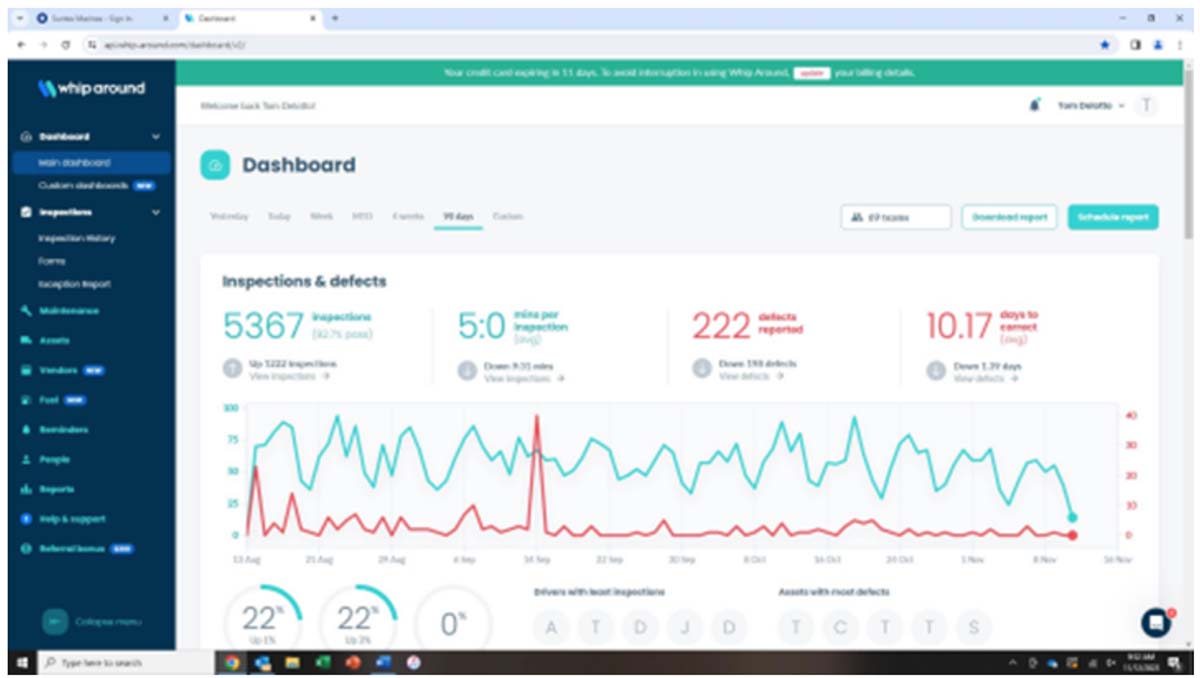
Hard Copy Missteps – Managing Your Marina via Digital Tech
Published on January 14, 2024As an industry, we must recognize how compliance and safety play into daily operations— must, not should or will or could if we had time. Let’s look at how some common marina operations are reflected in regulations and rules and how you can streamline compliance.
Record Keeping Avalanche
OSHA Inspections: Operators must comply with OSHA Standards for training and inspection of Powered Equipment. OSHA Powered Equipment inspections – 29 CFR 1910.178(q)(7) requires that “Industrial trucks shall be examined before being placed in service and shall not be placed in service if the examination shows any condition adversely affecting the safety of the vehicle. Such examination shall be made at least daily.”
This means every piece of powered equipment that moves or operates using an engine of some type (fuel or electrically powered), must be inspected prior to use. For marinas that could be a whole pile daily. Imagine managing a paper checklist system to inspect all powered equipment on the property each day if needed – forklifts, golf carts, tractors, mowers, trucks, work barges, and more.
NFPA NEC: Standards inspections under these headings are becoming more crucial daily. For instance, marina power systems need to be inspected for current leaks to prevent electric shock drownings. Insurance carriers may be using these standards to make decisions on whether or not to pay for claims.
Workers’ Compensation: Did someone sustain an injury on the job? Did your insurance carrier challenge you about not performing OSHA-required powered equipment training, which could have prevented the injury and their payout?
These are just a few examples of the mass of record-keeping marinas have to do. How many of you still rely on hard-copy checklists? You know that flurry of paper, a storm of documents that may or may not be completed, or is half done with notations, highlights, tears, scribbled upon, leaving something that looks like it went through the wash. Then that list may or may not be distributed or used in meetings or reviewed. In the end, it gets lost in a pile of other documents, filed, or misfiled.
Here’s the reality. Only 8% of frontline workers want access to print newsletters, brochures, handouts, and reports. Even less want to carry around and fill in 20 sheets of dock walk paperwork. Statistics provide ample ammunition for digitizing marina management cultures. The technology is obviously there, as well as a growing popular acceptance of said technology.
Our focus here will be how the digital groundswell can make marina operators’ lives better by replacing all the hard copy missteps.
Below is a list of activities that you should be keeping records of at your marina. If you answer “yes we use paper to track any of the below, you might want to keep reading.
How does your team run dock walks?
How many slips and dry storage spots are checked?
How do your teams currently inspect, report, record and respond to marina liability? Hazards like rotten deck boards, broken ramps, trip hazards, or any other site location problems could lead to a customer or employee being injured and a potential lawsuit.
How are teams inspecting restroom facilities to ensure they are cleaned and maintained routinely?
Electrical Safety
Inspecting and recording electrical leakage testing of all slips – NEC Reg;
Inspecting power pedestals for wear and damage;
Inspecting, testing and recording GFI outlets monthly NEC Reg.
Fire Prevention
Recording Regular Dock inspections for ALL Hazards.
Inspecting Exit Signs and emergency lighting in buildings. Monthly Fire extinguisher & Fire Control System inspections per NFPA & OSHA 1910.157.
FUEL Dock Operations
Inspecting dispensers, sumps, and control equipment;
Inspecting transition & monitoring sumps; Conducting EPA mandated AST UST inspections monthly.
OSHA Powered Equipment Training
Inspecting powered equipment daily per OSHA Standards.
I am sure the prior list provokes reactions like “Yeah, we always stay on top of our to-do lists, checklists, reviews, and customer inputs.” Or the listing stimulates an internal debate on the flaws of how the team is currently managing or not managing property activity using a hard copy paper document system of checklists. Or maybe, one of your progressive thinkers is building another Excel spreadsheet.
Digital Solutions
Now for a solution. We live and work in a constantly evolving digital world where digital is everywhere, texting is king, and emails form the basis of daily office life. Statistics back up digitizing wherever possible:
33% of adults and 77% of 18-28 year olds prefer digital work platforms;
67% of employees use their personal devices for work;
The shocking statistic above is that while marinas and boatyards are brimming with digital processing such as contracts, dry stack launches, and service work orders, the need as well as ease of implementing digital compliance inspections and safety is missing.
Good business owners should want to improve profitability, be safe, comply with federal standards, save time, and increase productivity gains. To make this work, selling the idea of digital processing is going to have to occur to get employee and management buy-in for digitized compliance and safety implementation. Show your team how digitizing makes the job easier with a higher rate of success. Explain how they’ll be doing less work for the same amount of time invested and it’s simpler to accomplish.
Digital Inspection
The Suntex Team has been working for the past 18 months to streamline our digital processes. There are several companies that offer digital solutions and we chose to work with a company called Whip Around. I can conservatively say I find another use for the app each week that makes marina management simpler, more efficient, and improves team morale.
While fear of costs and complications may keep marinas away from digitizing, I’ve found the opposite. Our service is economical and allows users to inspect, file in the cloud, highlight flaws found for repairs, and manage the team to make sure the tasks are getting done. An infinite number of inspection files or pages can be added with the app enabling templates and inspection forms to be embedded and assigned to an asset.
Consider for a moment the many inspection forms you may need: Forklifts, Mowers, Road Trucks, Gators, Golf Carts, Powered Crane Barges, Work Boats, Rental Boats, EPA Mandated AST / UST Inspections, Buildings, Fuel Docks, Slip Power Pedestals, OEM Warranty, Tractors, and on and on.
The only equipment required to install Whip Around is a phone or tablet to which you install an app. Phones allow for true remote flexibility, while tablets are useful for asset inspection in the field where tablet cameras and large screens better support data entry.
With the app installed, you can set up a dashboard with global oversight of all activities, monitoring single site activity or multiple site actions. There is no limit to how many people can be added to the system and adding them is simple.
To help assure success with a new digital platform, engage your teams in training. All your folks use a whole universe of apps, so this step should be a piece of baklava.
Categories | |
Tags |