Marinas Turn to Wastewater Treatment Systems to Achieve Water Authority Compliance
Published on February 20, 2020All marinas must meet EPA and local wastewater requirements for effluent, including those under the Clean Water Act. Failing to do so can result in severe fines that can quickly escalate. Bilge water, which can contain oil and other contaminants, is one common source of wastewater.
Another source of considerable wastewater involves the use of anti-fouling bottom paint on boats. The lead, zinc and copper in anti-fouling paint, which ends up in wastewater, must be dealt with to stay in compliance with regulatory standards.
To meet regulation standards, many marinas install a wastewater treatment system to separate the contaminants from the water so it can be discharged. Although paying to have such wastewater hauled away is also an option, it is expensive. Many marinas opt to treat the wastewater at its source. The water can return to the source, and treated sludge passes a TCLP (Toxicity Characteristics Leaching Procedure) test and can be disposed of as non-hazardous waste in a local landfill. Fortunately, complying with EPA and local wastewater standards has become much easier with a variety of more fully automated wastewater treatment systems.
Automated Treatment
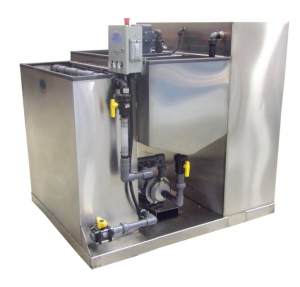
In contrast to labor-intensive multiple step processes, automated wastewater treatment can help to streamline production, usually with a one-step process. The systems usually have a large upfront cost, but save money in time and efficiency for many years.
An automated wastewater treatment system can eliminate the need to monitor equipment in person. On their own, automated systems separate suspended solids, emulsified oil and heavy metals, and encapsulate the contaminants, producing a de-waterable sludge. The water is typically separated using a de-watering table or bag filters before it can be discharged. Other options for de-watering include using a filter press or rotary drum vacuum. The resulting solids are non-leachable and are considered non-hazardous.
These systems are available as manual batch processors, semi-automatic and fully automatic systems. In some cases, it can be faster and more cost effective to add to or modify a marina’s existing wastewater treatment system. Because every wastewater stream is unique to its application, each wastewater treatment solution must be suited to or specifically tailored to the application.
The first step in evaluating the potential cost savings and effectiveness of a new system is to sample the wastewater to determine its chemical make-up, followed by a full review of local water authority requirements. The volume of wastewater that will be treated is also analyzed, to determine if a batch unit or flow-through system is required. Other considerations include the size restrictions so the system fits within the marina’s available footprint.
Mystic Shipyard
At Mystic Shipyard, in Mystic, Connecticut, the marina uses a semi-automatic wastewater treatment system.
When the marina does bottom cleaning on boats to remove growth such as barnacles and algae, the pressure washing process also removes anti-fouling paint, which contains metals and biocides, such as lead, zinc, and copper and suspended solids, that are released into the washwater.
To treat this wastewater, Mystic Shipyard turned to a 250-gallon batch tank, bag filter tank, and Cleartreat® separating agent from Sabo Industrial Corp., a New York-based manufacturer, distributor and integrator of industrial waste treatment equipment and solutions, including batch and fully automated systems, separating agents, bag filters, and accessories.
The wastewater is pumped to the 250-gallon mix tank, where a float disengages the catch basin sump pump to prevent overflow. Ten pounds of the separating agent are added at a 0.5 percent introduction rate to create large sturdy floc. The treated effluent is then transferred to the bag filter tank for sludge filtering. The tank’s four independently operated bag manifolds enable continuous use and maximum dewatering.
The sludge produced is captured in the bag filters and can be disposed of in a local municipal landfill. The sludge will not break down and will not return the contaminants to the water supply. The treated effluent is collected in the tank for discharge to the sewer system or is suitable for reuse.
According to Jeff Marshall, president of Mystic Shipyard, the SABO RT250 Cleartreat clay system was the right choice for many reasons including reliability and ease of operation. Most important, he says is that it produces an end result well below the state standards and sewer authority requirement for discharge to the sewer. Marshall said not having the cost to haul the wastewater away over a year, paid for over half of the initial investment for the treatment system.
Separating Agents
Even the most advanced automated wastewater treatment systems require effective separating agents, which agglomerate with the solids in the wastewater, so the solids can be safely and effectively separated out.
In its line of Cleartreat wastewater treatment chemicals, the separating agents from Sabo Industrial use a special type of bentonite clay, which is formulated to break oil and water emulsion, provide heavy metals removal, and promote flocculation, agglomeration and suspended solids removal.
Bentonite has a large specific surface area with a net negative charge that makes it a particularly effective adsorbent and ion exchange for wastewater treatment applications. It has the ability to swell 16 times its normal weight when introduced and mixed with wastewater. As such, bentonite is essential to effectively encapsulate the materials. This can usually be achieved in one-step treatment, which lowers process and disposal costs.
After using separating agents, typically a valve is opened and the treated effluent is pumped through a bag filter, de-watering table, rotary drum vacuum, or other type of filtration. The floc or sludge stays in the bag and the clear water passes through.
When the bag finishes dewatering, the pumps are usually left on because bentonite is hydrophobic, which means that it continues to shed water when removed from water. So, over time it will become extremely hard and pass any TCLP test. In fact, copper, lead and zinc become virtually undetectable in the treated wastewater and encapsulated sludge.
A similar wastewater treatment approach is also being considered to treat bilge water.
Traditionally bilge water is vacuumed from boats and stored in barrels, which are hauled away at a cost of nearly $2.00 a gallon. Instead, marinas can use wastewater treatment at an estimated cost of about $0.30 a gallon.
With today’s advanced automated wastewater treatment systems, and effective separating agents, such as Cleartreat, marinas have easy and economical means to remain compliant with local ordinances and the EPA.
Sal Boutureira is the owner of Sabo Industrial Corp., in New York. Sabo can be reached at 845-562-5751 or by email at info@saboindustrial.com.
Categories | |
Tags |