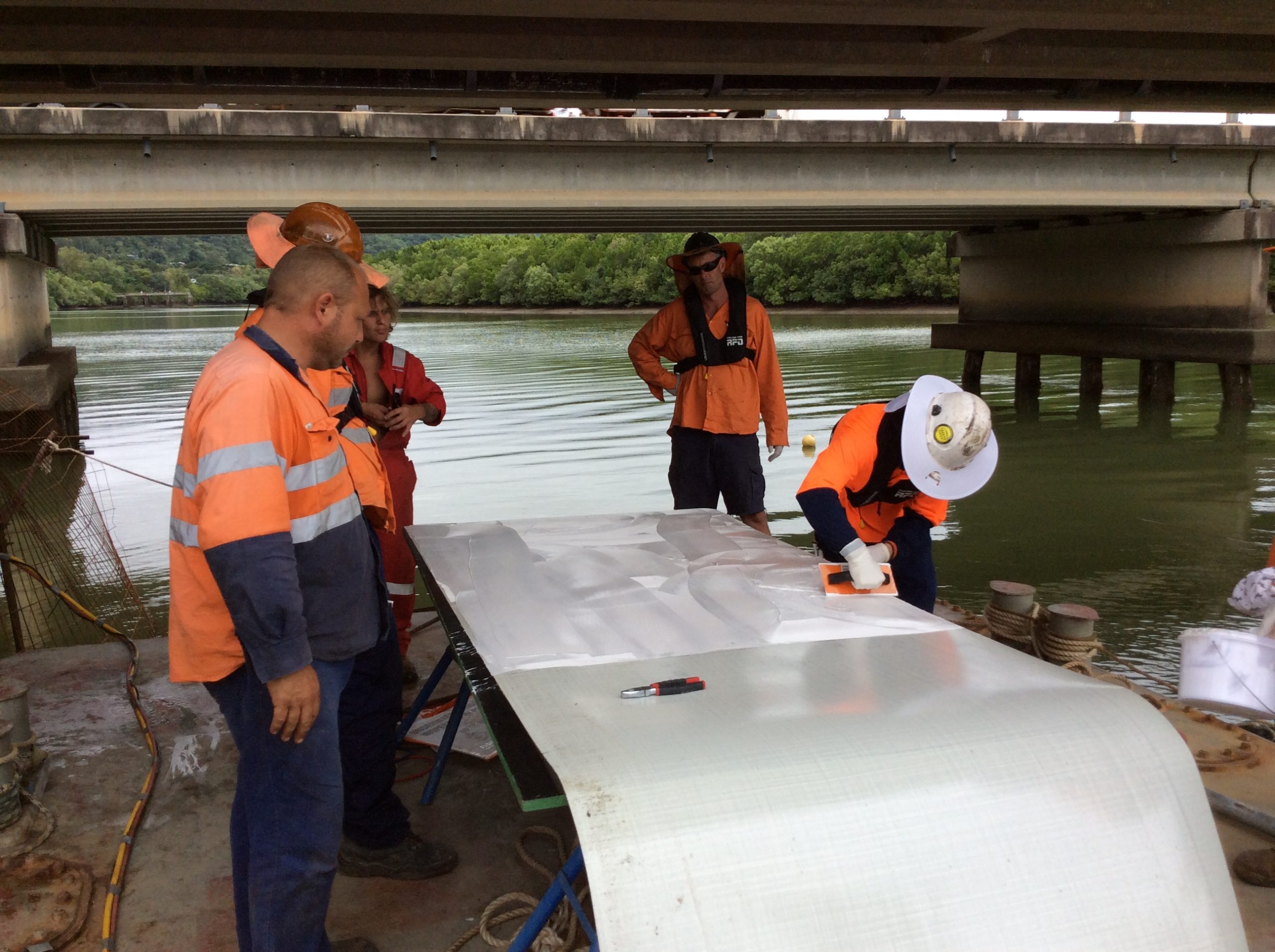
New Advances in Repair and Strengthening of Piles
Published on March 5, 2023Submerged piles always corrode with age and lose their initial load-carrying capacity. When replacement is not an option, these piles have been traditionally repaired by encasing them in a fiberglass shell that is filled with concrete. These forms require advanced ordering, are bulky to ship and store, and provide little structural benefit. After more than three decades of development and multiple U.S. Patents, the PileMedic® system can be an alternative to traditional methods.
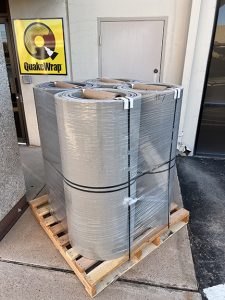
Main Advantages
Unlike typical laminates that are four feet wide and are supplied in 100-foot-long rolls, PileMedic® is a new type of Fiber Reinforced Polymer (FRP). A single pallet of PileMedic® contains 1,000s of square feet of laminate, enough to repair more than 50 piles. The main advantages of the laminate compared to conventional fiberglass forms include:
Strength – PileMedic® laminates are up to two to three times stronger than steel.
Size & Shape – The 0.05-inch-thick laminates are flexible enough to be wrapped around piles of any shape and size. In the field, a length equal to twice the perimeter of the pile is cut from the long rolls. The second half of the laminate is coated with a special epoxy paste, and it is wrapped around the pile onto the first layer to create a two-ply structural shell around the pile. This eliminates the need for custom ordering the jackets, saving significant time, and shipping and storage costs. The annular space between the jacket and the pile is filled with grout, concrete, or epoxy grout later.
Confinement – The unique seamless jackets apply a uniform confining pressure 360 degrees around the pile. This increases the strength of the timber or concrete pile significantly and is a benefit that cannot be achieved with conventional fiberglass forms. Many strengthening projects call for placement of longitudinal bars and ties around the pile. These rebar cages are bulky and must be handled by two or more divers. PileMedic® jackets also eliminate the need for lateral ties, allowing the divers to install the vertical reinforcing bars individually (when needed). The elimination of handling assembled reinforcing cages that requires two divers, results in significant cost savings for the project.
Corrosion Protection – It is well recognized that the oxygen present in water is the fuel for the corrosion process. The laminates create a seamless and impervious shell around the pile, preventing any moisture or oxygen ingress. This will drastically reduce the corrosion rate in the pile.
Enhancements to Construction
The U.S. Navy is among many clients who have used the repair system. Several accessories have been produced that enhance the quality of construction and result in more accurate engineering design:
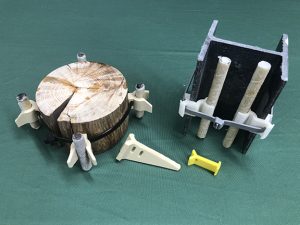
Spacers – These plastic parts are available in many shapes and sizes and serve multiple purposes. Divers can pass a zip tie through several spacers and fasten them around the pile. The longitudinal reinforcing bars (typically made of non-corroding glass FRP) can be snapped into place. This allows the engineer to know the precise location of each bar to calculate the strength of the retrofitted pile. The spacers also define the annular space between the jacket and the pile that will be filled with grout or concrete. In some cases, the repair portion of the pile extends into the mud line and the soil provides a seal at the bottom of the jacket for placement of the grout. However, there are many applications where the length of the repair is limited to the splash zone, requiring the creation of a seal at a point along the height of the pile where the jacket terminates. The skirt pin allows the creation of that seal.
Shear Transfer in Steel Piles – The relative smooth surface of steel piles inhibits bonding of any concrete encasement to the host pile. The patented ShearWrap® and ShearClamp® overcome this shortcoming and eliminate the need for any welding on the jobsite. Engineering calculations determine the size and number of these elements needed for each project.
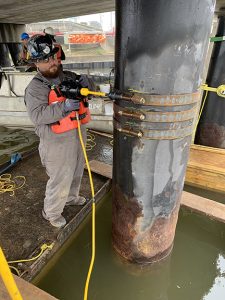
Successful Test Results
The PileMedic® system has been tested by several government agencies. Caltrans conducted tests of concrete bridge pilings, which were severely damaged in an earthquake. Texas DOT conducted a study of corroded steel H-piles at the University of Houston. Even sections with up to 80% section loss gained their full strength after being repaired with the system. The Nebraska Department of Roads has also studied the repair of timber piles used in the state.
More recently, the U.S. Army Corps of Engineers (ACE) conducted a major investigation of solutions for exigent repair of piles. Based on full-scale tests, ACE selected PileMedic® for the U.S. military to repair timber, concrete, and steel piles worldwide. As a part of this evaluation, 90 concrete piles were repaired at Pearl Harbor in Hawaii. The installations also considered various conditions such as poor visibility in the water and water current. As noted by some of the diving team members, the new system reduces the repair time to as little as 1/3 of the previously used pile jackets. Considering that the labor/diving fees account for about 75% of the total repair costs, PileMedic® could result in significant time and cost savings in pile repair projects.
Field Installation
PileMedic® has been installed in many projects worldwide. Among these include over 500 timber piles at Perdue Agrobusiness in Chesapeake, Virgina, where some piles had 100% section loss. Ninety concrete piles were used for the Port of Seattle. Houston installed 95 steel piles, Indiana DoT used 265 steel piles, and 100 piles were used in a jetty belonging to the Nigerian National Petroleum Corporation. In addition, piles have been used at numerous bridges in Australia, a pier in Vietnam damaged in a mooring accident, and by the U.S. Navy in the repair of a pier in Ukraine.
Mo Ehsani, PhD, PE, SE, is president of QuakeWrap Inc. and centennial emeritus professor of Civil Engineering at The University of Arizona. He can be reached at mo@quakewrap.com. Full details of the system are available in two recent webinars that have been recorded and can be download at www.PileMedic.com/webinars.html
Categories | |
Tags |