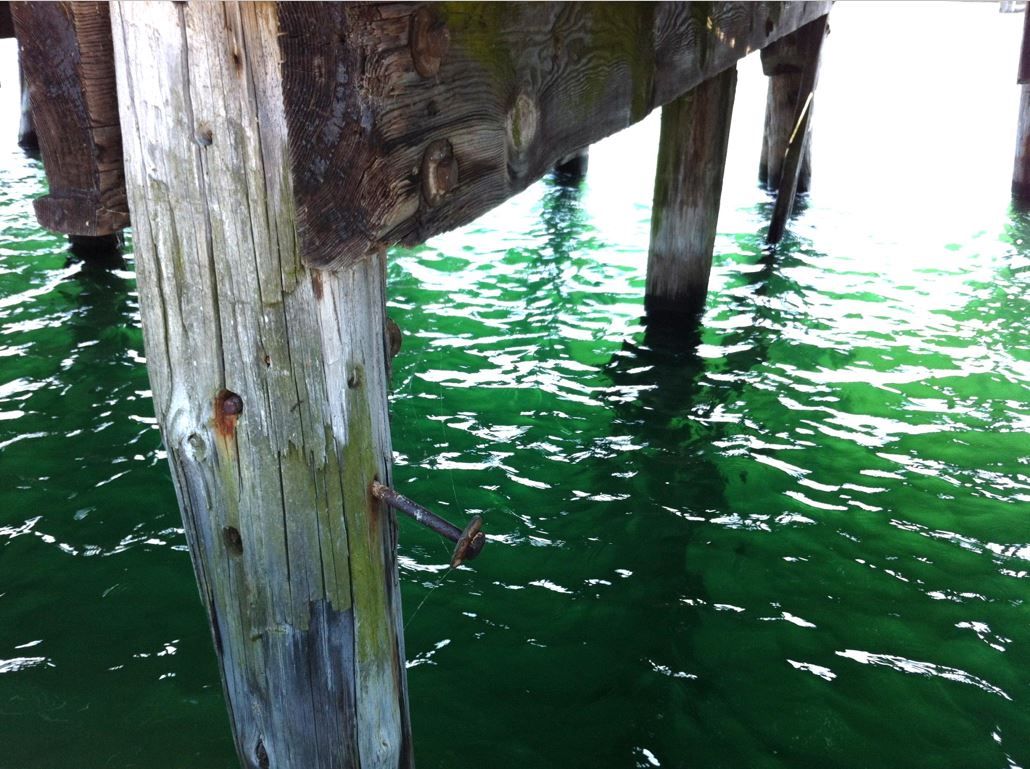
Strategies for a Comprehensive Facility Condition Assessment
Published on May 1, 2020There are many reasons for marina owners to complete a comprehensive condition assessment of their facilities, including ensuring the safety of staff and customers, reducing insurance and liability concerns, and of course improving profitability and maintaining the reputation of the facility with the boating public.
For those who are considering buying a marina, they will want to know as much as they can about the quality and condition of the physical infrastructure so they will have a good idea of how much useful life is remaining in the various marina systems. This will allow existing owners and buyers to confidently plan long-term capital expenditures, and if the bank or investors require a capital reserve study, a comprehensive condition assessment will be key to completing that process and helping ensure the long-term financial health of the business.
Where to Begin?
To start the process, we recommend collecting all available surveys, drawings, specifications, plans, permits and engineering studies. Construction drawings from the engineers and architects will make future renovations easier to complete and less costly to design, and shop drawings from the dock fabricator will make it much easier for staff to locate hidden utilities in docks and make repairs when needed.
Equally important, these drawings will help clarify the age of the facilities and when renovation projects were completed, which is helpful in determining the remaining useful life of the infrastructure. While many floating dock systems have an expected service life of 25 to 30 years, the useful life could be longer or shorter depending on the wave climate of the facility. On the other hand, fixed dock infrastructure and steel pile walls can last up to 50 years or more, and the drawings and specifications for a steel frame system will tell the engineer what the original steel material sizes were. The current steel thicknesses can be measured and compared with the installation date to determine the rate of deterioration and estimate remaining useful life.
If geotechnical borings and soils reports were prepared for the original design of a facility, that information can often be used for future projects, potentially saving thousands of dollars in new engineering studies. Copies of permits, especially for maintenance dredging or phased expansion projects, are very important as permits typically are valid for a set number of years. Extending or renewing an existing permit must be done before the permit expires and is much less expensive and time consuming than submitting an application for a new permit.
The next step is based on the goals of the marina owner. If the primary goal is to ensure immediate safety and reduce liability, then we recommend focusing first on potentially high liability items like the marina electrical system, fuel system and compliance with the Americans with Disabilities Act (ADA). Longer term planning for renovations and expansion would involve more detailed assessment of the marine structures, bathymetry (water depths), pavement, landside utilities and buildings.
Electrical and Utility Systems
While increased awareness of Electric Shock Drowning (ESD) in the boating community has hopefully encouraged more boaters to have their boats inspected and reduced the number of people swimming in marinas, it has also increased the potential liability to marina owners. We recommend a comprehensive inspection of the marina electrical utility systems by a qualified licensed electrician or engineer every year, either before the marina opens for the season or just prior to the peak season in facilities that are open year-round.
With current record high water levels on the Great Lakes, many facilities are finding their junction boxes flooded. In our work inspecting marina facilities, we have found evidence of hidden electrical fires, worn cables with exposed conductors in contact with metal dock frames, and water leaks inside electrical panels. In older facilities, we have found standard 120v receptacles mounted at ground level adjacent to the water without ground fault protection or in-service covers, located right where someone reaches to pull themselves out of the water. At minimum, marina staff should identify any damaged pedestals, lights, receptacles, junction boxes, or any other equipment during their daily inspections and immediately shut down systems where appropriate until they can be repaired. Regardless of code requirements, we recommend all facilities consider adding ground fault protection.
A similar inspection of pumpout systems, potable water, and fuel tanks and distribution systems should be performed regularly.
• Is the sanitary line from the pumpout system securely anchored to the dock or is it leaking?
• Are the required vacuum breakers in place on every hose bib?
• With record high water levels, are the utility lines suspended beneath the fixed docks submerged?
• Are they at risk of being encased in ice during the winter, and subsequently damaged when water levels change?
All of these issues are much easier and less expensive to deal with before the damage, leak or injury occurs.
Americans with Disabilities Act Compliance
In 2010, formal Americans With Disabilities Act (ADA) “standards” for recreational boating facilities were established, replacing the earlier accessibility “guidelines.” The distinction between the two is important, because all marinas that are open to the public are required to comply with the ADA standards. A facility that complies with the earlier guidelines does not automatically comply with the new standards as a “grandfathered” facility. If a facility was built before 2010 and no specific ADA improvements have been made, it is likely that the facility is not in complete compliance. Fortunately, we very often find that most facilities can come into compliance with a few relatively simple and reasonably priced improvements.
The key issues to confirm include:
• appropriate width and slope accessible routes;
• having at least one accessible slip of at least five foot width for broadside access;
• dispersion of accessible slips throughout all types of slips offered;
• appropriate reach range measurements for utility pedestals – which, for the majority of marinas is the most common issue;
• gangway slopes being too steep at low water for marinas with floating docks.
Fixed Structures
Inspecting fixed dock and wall structures below the waterline may require a dive survey depending on the type of piles or structure. For piles, we often find the worst damage present at the water line, particularly in the “splash zone” where changing water levels from tides, waves and normal fluctuations mean pile materials are constantly getting wet and then drying out. Crib structures made of timber and filled with stone may fail below the water line and allow the fill materials to spill into navigable areas, and older timber piles may fail at the mudline. In addition, steel sheet pile walls or their tie-back systems can fail below the waterline, allowing subsidence of materials behind the wall that can cause structural failure of walks and utility corridors, so a dive survey overseen by a licensed Professional Engineer (PE) should be considered on older facilities. For a quick survey, marina owners could use a GoPro style submersible camera mounted to a pole if the water is clear enough for photography.
Above the water, look for obvious signs of deterioration, such as cracked or rotted timbers in wood frame systems; and rust, flaking paint, bent members and failing connections in steel systems. Look for loose decking and cleats, and be sure to open up portions of the decking to inspect the underside of the framing. If possible, inspect the underside of the docks for failing utility lines and hangers. If any significant damage to structures is found, we recommend contacting a qualified, licensed engineer to prepare a properly designed repair.
Floating Docks and Anchorage
The inspection of floating dock systems must include the decking and structure itself, the floatation elements, and the anchorage elements. Each type of floating system, such as steel, aluminum, wood or concrete, will have its own particular areas that require more maintenance and care than others, so it is important to engage the dock supplier if possible (if you haven’t operated a particular system in a facility you’re considering purchasing.) Be sure to inspect the connection systems between dock sections, and either have a diver check the flotation or at minimum use the camera method.
For pile anchored systems, inspect the piles as described above for fixed docks, and be sure to check the condition of the pile guides and all associated fasteners. For chain and anchor or flexible elastic style mooring systems, be sure to have a diver check the condition of the chain, lines and all submerged anchoring elements, along with the mechanical connections to the anchors, for corrosion and wear. Check with the manufacturer on the lifespan of all elastic elements to be sure they are within their acceptable lifespan and determine when they’ll need to be replaced.
Putting It All Together
Going through this process can be a bit overwhelming, but learning as much as possible about the condition of a facility is a part of a very powerful planning tool for marina owners. Next issue, we will explore how to assess the information collected and start setting priorities to make smart decisions on where to invest renovation budgets to best effect.
Greg Weykamp, ASLA, LEED AP, president and principal at Edgewater Resources, LLC. He can be reached at gweykamp@edgewaterresources.com or by phone at 269-408-6562.
Categories | |
Tags |