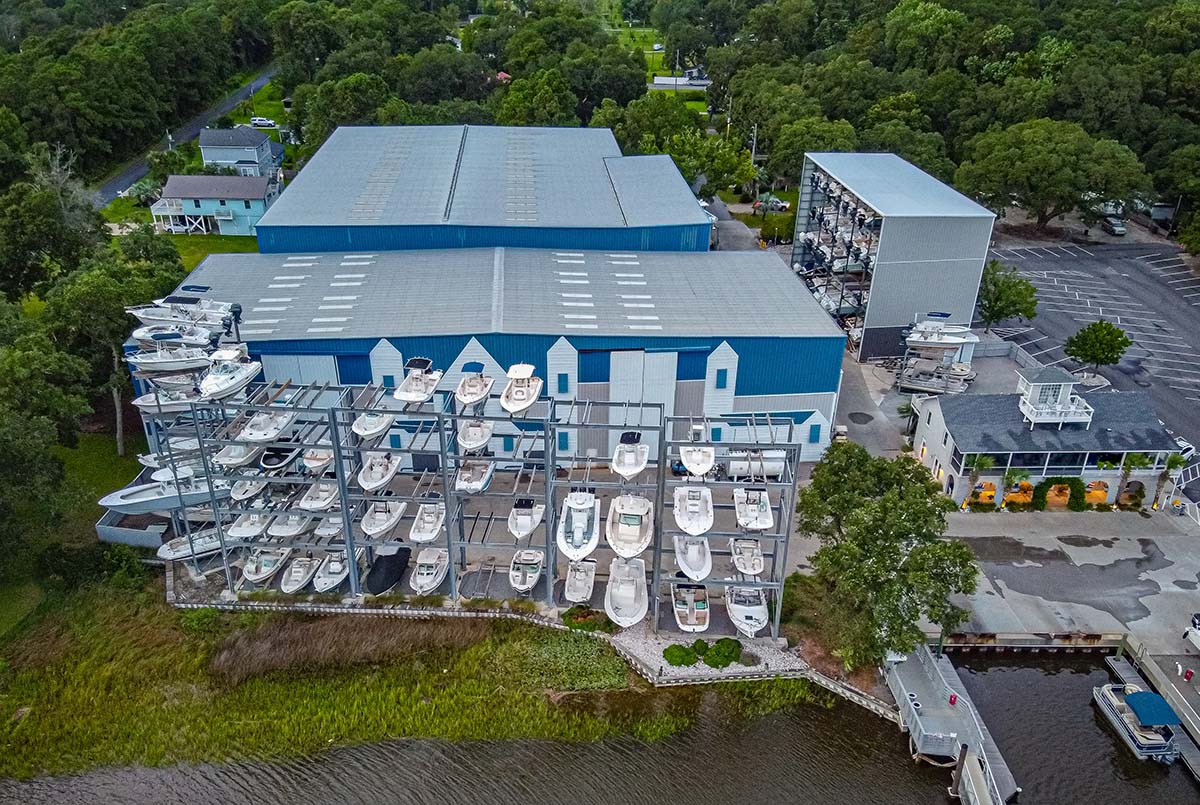
The Ins, Outs, Ups and Downs of Rack Storage
Published on April 7, 2024Whether you call it rack storage, dry rack or vertical marine storage, it has come a long way over the years.
This storage has evolved from the early approach of using wooden posts for two levels of boats with converted front loaders and extended forks, to now fully enclosed buildings that can be multiple stories high with steel racks, specialized lifts and even fully automated systems.
Of course, the biggest argument for rack storage is that it allows for the efficient revenue-producing use of upland real estate by allowing for multiple layers of boat storage within the same footprint. It started with lighter boats in the 15-foot to 20-foot range and has evolved to where boats up to 60 feet long, with weights that can be upward of 40,000 to 50,000 pounds, can now be handled.
As rack storage system options have increased, the types of boats that may be desiring rack storage have also dramatically changed. They have gone from the relatively shallow flat or shallow “v” bottom runabouts with an outboard motor, to boats with deep “v” bottoms and multiple outboards with trim tabs, inboards with rudders and skegs, longer boats with higher freeboards or fixed towers, and even cruising boats – along with dramatic weight increases.
Understanding Boating Trends
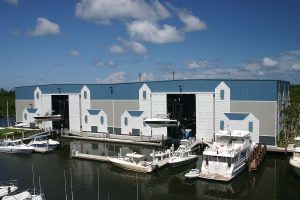
When contemplating rack storage, one needs to understand the surrounding user market as it is today and the boating trends projected for tomorrow, as well as changes in the climate. Some typical boat size trends being seen in the industry include moving from what may have been the historic maximum of 28 to 35 feet to often having a minimum of 30 feet and going up to 55 or more feet, particularly in coastal areas, including large lakes. In the inland river and smaller lakes market, the target seems to be toward a minimum of 25-foot to 30-foot boats, with a growing presence of boats and a corresponding need for boat rack storage in certain areas for 35-foot to 40+-foot boats. Width, length and weight requirements continue to be on the upswing, and there seems to be a trend to include larger boats with non-collapsible bimini tops and towers, which require taller racks. All these differences require more thought and flexibility, while offering the potential for more revenue.
From the boater’s point of view, there can be advantages to rack over in-water storage. Painting the bottom of a boat becomes obsolete since the vessel is out of the water. Rack storage also prevents fading of the gelcoats and other materials. Owners also don’t have to worry about covering their boats; and there is always someone available to get the vessel ready for a trip and haul it in when a day on the water is over. As well as putting the boat away, rack storage can include valet services such as rinsing the bottom, flushing the engines and cleaning the rest of the boat.
Of course, there can also be disadvantages, such as dripping from boats above, the inability to work on your boat whenever you want, scheduling a launch, and perhaps the biggest of all, not being able to relax on a boat while on the slip.
Location, Location, Location
Is rack storage for every site? The simple answer is no. It can be effective and economically desirable, but one must do their homework and understand the pros and cons. We always say that every site is site specific, and that goes double for rack storage.
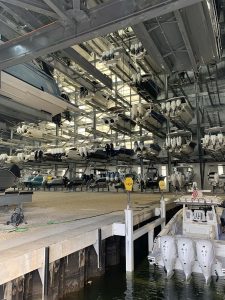
However, as a general approach, there are two major pieces to the rack storage jigsaw puzzle: is it compatible with the location and is it economically desirable for the site?
Site location compatibility is a big deal. Many do not consider this up front and then get frustrated when going through the regulatory process. In most areas there are zoning regulations, and in many places quite restrictive regulations, including bulk and height constraints as well as parking, architectural treatment and setback requirements, which can significantly limit the size, height and economics of the rack storage structure(s). Neighbors may also voice disapproval at public hearings. Some communities, such as Fort Lauderdale, Miami and several in the Florida panhandle, have found ways to have peaceful co-existence, but, as areas become more populated and built up with residences, these issues may become more prevalent. Many communities, particularly in suburban areas, have height restrictions of 35 to 40 feet, translating to two to four racks high, depending on the size and type of boats one desires to place in the racks. Of course, there are some notable exceptions, particularly in more urban/city settings, such as Fort Lauderdale, where a recently opened facility is six racks high and 135 feet tall.
Rack Options
With respect to the racks themselves, today there are many choices:
Open racks: No sidewalls or roofs, often include smaller individual racks that can be portable and are viewed as equipment as opposed to a structure for approval purposes;
Roof covered racks: Protect vessels from some outdoor elements, including sunlight;
Roof and walls covered racks: Provide better protection from the elements and improved boat security. This option can be helpful when the land doesn’t lend itself to a full aisled building with racks on each side;
Fully enclosed rack buildings: Keep boats protected from outdoor elements, theft or damage. If hurricane rated, they also help obtain boat insurance and better coverage and rates.
Most rack systems are designed as rectangular or square with a perpendicular boat entry and exit. However, particularly in a retrofit project, the racks can be made angular, allowing longer boats to fit in spaces designed for shorter boats.
Adding to the puzzle there are two basic types of storage systems: mechanical with a negative forklift system or automated systems. All need to be maintained and serviced, although the issues and cost of each system vary greatly. A marina needs to consider the market and know the number of boats that can be moved/launched/retrieved in an hour. If one cannot keep up with the demand, then one is losing money and upsetting the customer base.
Forklift versus Automated
The forklift system is relatively simple and conceptually less expensive to implement. A basic system is usually quicker to get up and running and can be expanded relatively easily over time. It does not need a different piece of equipment for hauling and launching. More than one forklift provides backup in case one has a mechanical problem and allows for more than one truck to move boats in and out at the same time. We find that once a facility exceeds roughly 60 boats, having that second forklift becomes more of a necessity than a luxury. Forklifts need OSHA-certified operators with a skilled eye to place the boats in and out of the racks. (The OSHA certification is not overly difficult to obtain. A heavy, reinforced concrete surface is also necessary. The forklift makes noise (beeping) when moving in reverse, requires wide turning areas to move the boats and has greater weight limitation (more so than length) on how high boats, especially heavier boats, can be safely lifted. The forklift operator is on the machine, usually at the ground level, and the line of sight is diminished as the boats are lifted higher into the air.
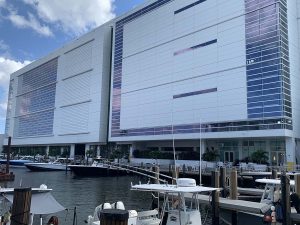
Automated approaches have not been as prevalent in the industry to date but are continuing to evolve, and there are many impressive new facilities. Currently there are four basic types of automated systems: overhead crane, overhead cables, bottom-mounted crane and a potential new automated vehicle transport system (like the automated pallet car elevator systems).
Each has its attributes and limitations. Some use traditional racks, some use five-walled cubicles, and there are variations upon a theme. Some can increase the heights and boat weights that can be lifted to higher levels much more than traditional three to four levels, reaching as high or higher than six to eight storage levels. All use various types of sensors and electronic controls and run from semi-automatic to fully automatic with just the press of a button.
The automated systems do have a narrower turning aisle than the forklift systems and reduce or eliminate the reinforced concrete turning aisle within the building. They are quieter than forklift operations and reduce manpower labor and human error either by always having an operator at eye level with the boat or by being fully automated, essentially eliminating the operator altogether. They can place heavier boats at higher elevations and can be placed using less space for the moving of the boat in and out of the racks.
However, automated systems often seem to have multiple vendors involved, including for traditional building components, software, sensors and other equipment. They often use a second piece of equipment to haul and launch the boats and then transfer to the main automated system. The logistics of the building placement usually are more restrictive due to the need to be close to the water’s edge, and they are powered by electricity, making them vulnerable to associated disruption issues. To avoid electrical disruptions, it is important to consider installing a backup generator.
Typical Costs
Most of these systems will require higher up-front costs than some form of forklift-based system, but they can increase efficiency, which can prove less costly in the long run.
So, what are the typical costs? That’s a question often asked, but not easily answered. In our conversations with various suppliers of the different types of systems over the years, we find that there is no real consensus as to generic costs per boat. There are just too many variables that influence the calculations. The one thing that all suppliers seem to have in common is that they all agree that each facility is unique for pricing, and we absolutely agree.
That said, and recognizing there is no average facility, we have tried it. What follows are very rough estimates of the cost per boat for the different systems, arrived at by eliminating land acquisition, development costs, regulatory and other associated costs, and assuming only a bare bones building (with no fancy architectural treatments), and the boat handling equipment/systems.
Forklift systems:
Simple outdoor forklift/rack system: $20,000 to $40,000 per boat
Traditional indoor forklift/rack system: $35,000 to $55,000 per boat
Automated systems:
Overhead crane system: $55,000 to $110,000 per boat
Overhead cable system: $70,000 to $110,000 per boat
Bottom mounted crane system:
with traditional racks: $35,000 to $70,000 per boat
with five-walled rack system: $45,000 to $100,000 per boat
Automated vehicle transport system: $75,000 to $100,000+ per boat.
These compare to the similar rough average bare bones cost of an in-water slip of $40,000 to $75,000.
Again, these figures are far from gospel, and they do not include other major development costs, which are real and will significantly change the economics of a project. The type, height and weight of boats as well as the number of levels of the building will significantly alter the cost benefit and payback ratios.
Also note that many vendors are talking in terms of higher buildings to capture one’s interest in a particular system, but, at present, there are relatively few areas in the world that would either allow or welcome six- to 10-level boat storage buildings. To date, automated systems have tended to make the most sense for bigger, taller buildings, and forklifts have traditionally dominated the smaller and/or shorter buildings, open racks, etc.
Where to Start
So, where should you start if you want to explore rack storage? There is no one answer, but we suggest that the first steps should include:
A) Determining the local regulations that might apply in terms of limitations on height, coverage and parking as well as any other zoning/land use regulations that could affect the implementation of a rack system/building;
B) Reviewing the site for what areas could be used and what the soil conditions are, and;
C) Analyzing the local boating market and trends.
Thereafter, try to determine what might be best for your area. Next, come up with a concept approach of how high and how big the facility is that you would ideally desire, including the types of boats. Talk to different providers and ask them to supply a spreadsheet analysis of all component costs included for what you are contemplating. Some will even provide a spreadsheet with their interpretation of competitive systems. Land and site development costs may or may not be included in their spreadsheets but should be as part of your overall homework.
So, the bottom line is dry stack can be meaningful, but, like most development projects, one needs to really do one’s homework and fully understand the project. We would also suggest looking at the track record of the system being considered and having candid discussions with the potential supplier, as well as with others who are actively using the system for hands-on input. Each system has its own advantages as well as disadvantages, and one’s location is typically most important in determining which system might be better than others, including for the rate of return.
Dan Natchez, CMP, is president of DANIEL S. NATCHEZ and ASSOCIATES Inc. He can be contacted by phone at 914/698-5678, by WhatsApp at 914/381-1234, by email at dan.n@dsnainc.com or online at www.dsnainc.com.
Brett Roof is vice president of Roof & Rack. He can be contacted at brett@roofandrack.com.
Categories | |
Tags |