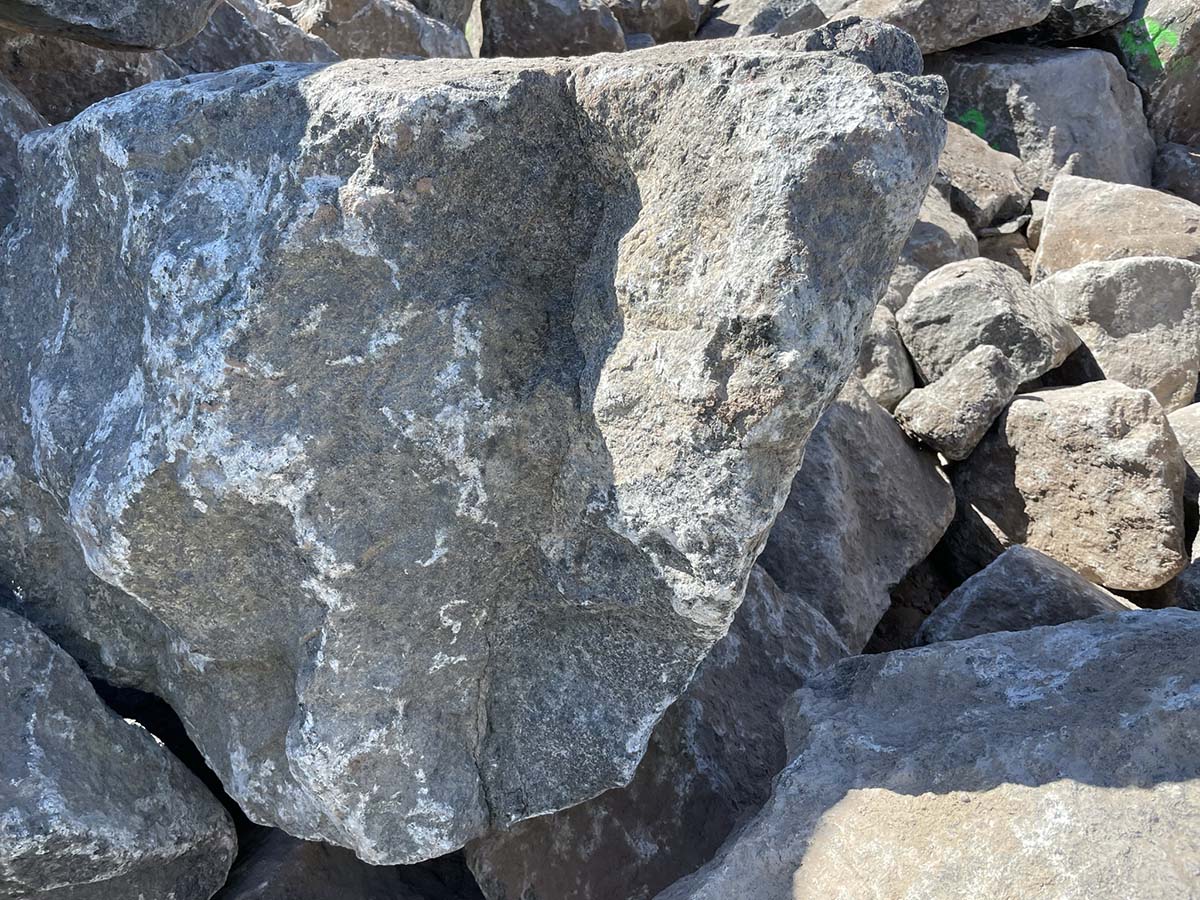
Everybody Must Get Stone: How to Make Sure it’s the Right Stone for the Job
Published on August 31, 2021With so many COVID-delayed construction projects now moving forward, natural materials such as wood and stone are suddenly in high demand – and more prone to shortages and price hikes. This is a particularly pressing issue for the marine industry. While it may seem like “a stone is a stone,” the need for a specific quality of stone is critical to protect shorelines in energetic wave environments and to sustainably build and upgrade existing marinas and harbors in response to recreational market demand and climate change.
With no signs of a slowdown in demand for quality stone on the horizon, and inexperienced contractors jumping in to fill the void left by fully booked marine construction specialists, it is more important than ever to know what to look for when purchasing stone. While cost per ton remains important, there is no benefit to saving money on junk stone that will be likely to fail after it is installed. How do marina owners make sure that what gets delivered to their construction site meets critical quality specifications and will achieve the level of performance required to protect their investment?
Good Stone Can be Hard to Find
Due in large part to an extended period of record high lake levels, quality stone is becoming hard to find for projects throughout the Great Lakes region. As contractors gobble up available stock in what seems to be a race against time and quarry owners work feverishly to meet demands, stone prices have risen sharply – increasing over 160% in the last year or two alone. While this pales in comparison to the price increases for lumber, stone for marine applications is a huge percentage of the overall cost for many large projects.
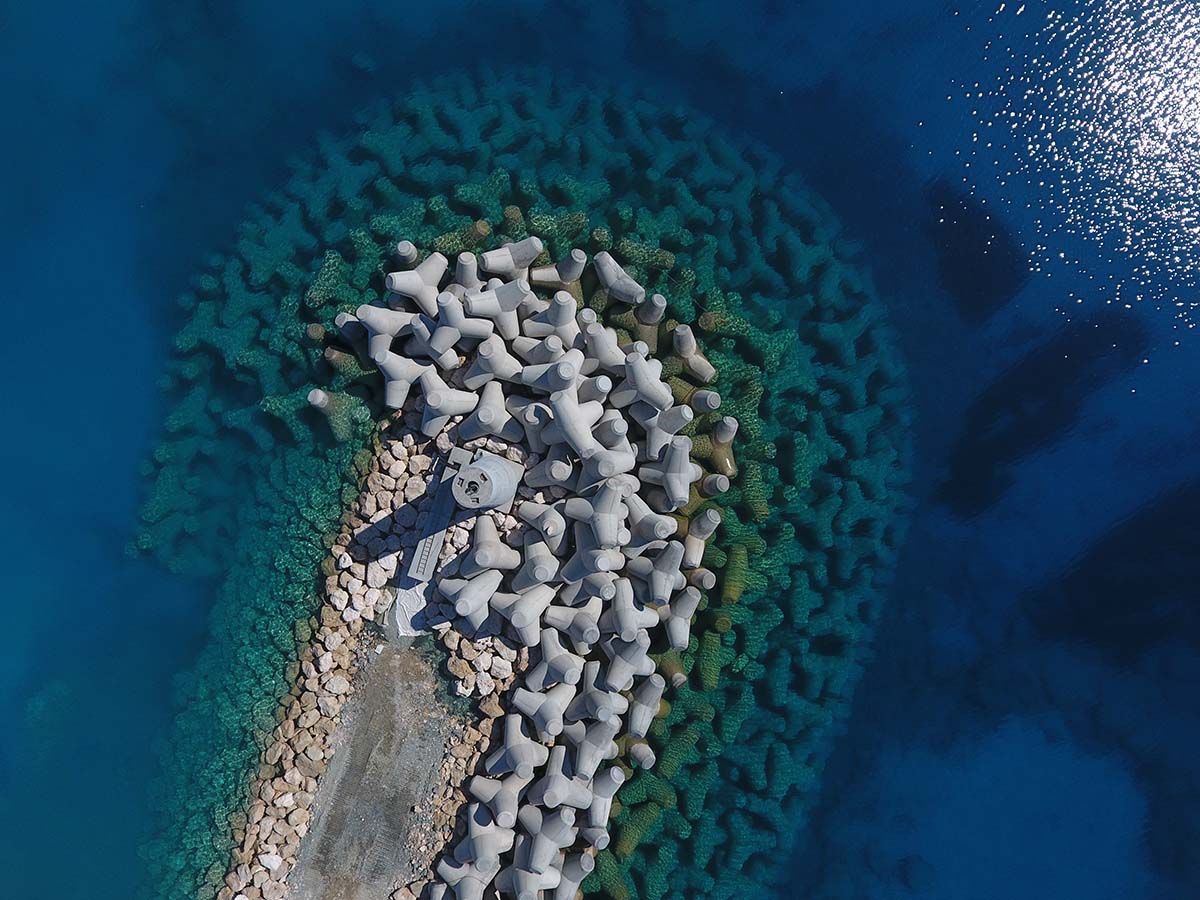
Outside of the Great Lakes and in places such as the Bahamas and Cyprus, good local or regional sources of stone may not even exist. In some cases, the stone that is available may be of insufficient quality or can’t be produced in large enough quantity or size to meet the requirements for marine-grade armor stone. In these cases it is sometimes possible to source inexpensive quality stone from other regions or countries and still get the desired cost per ton when shipping is factored in. For example, for the inner harbor portion of the Hoakalei basin project on the island of O’ahu in Hawaii, SmithGroup engineers were able to ship quality stone from China and still have it be cost effective. In contrast, for the Ayia Napa Marina in Cyprus, the cost to ship quality stone from Norway proved to be too much for the project budget.
In instances where quality stone simply doesn’t exist, or doesn’t meet the necessary specifications, here are a few options that can be considered:
• If quality material exists locally, but the density or specific gravity of the available stone is relatively low, stone sizes can be upsized to compensate. The same strategy can apply in situations where armor stone is more rounded instead of blocky, but in this instance the upsizing helps overcome the lower degree of resistance resulting from less interlocking of the breakwater and revetment stone construction. When compensating for reduced density by upsizing the stone, other properties must be checked thoroughly to assure durability, such as the stone’s compressive strength and resistance to weathering and abrasion.
• If quality material doesn’t exist, and it isn’t practical or cost effective to ship from the closest source, then alternative materials can be explored. In the case of Marina Pez Vela in Costa Rica, sheet pile could feasibly be used as the replacement. In other cases, concrete armor units such as Accropodes or Tetrapods may be a good solution.
For Ayia Napa Marina, some local stone was available, but the amount was very limited and what did exist could not be quarried to generate stones in the 25-30 ton range. Project designers used concrete armor units – 20-ton Tetrapods with a specified placement pattern to achieve high interlocking – and were able to attain roughly the same stability that would require 50-ton stones.
Knowing What to Look For
While many organizations such as state DOTs have established stone specifications that drive production at many quarries, these road-grade aggregate and quality requirements don’t readily translate to marine applications. Since there is no one-size-fits-all armor stone, or for that matter one specification that will work with all the variables that influence the size and placement of that stone, one can be left wondering what “quality stone” means for a particular job and how best to determine if you’re getting what you’ve paid for.
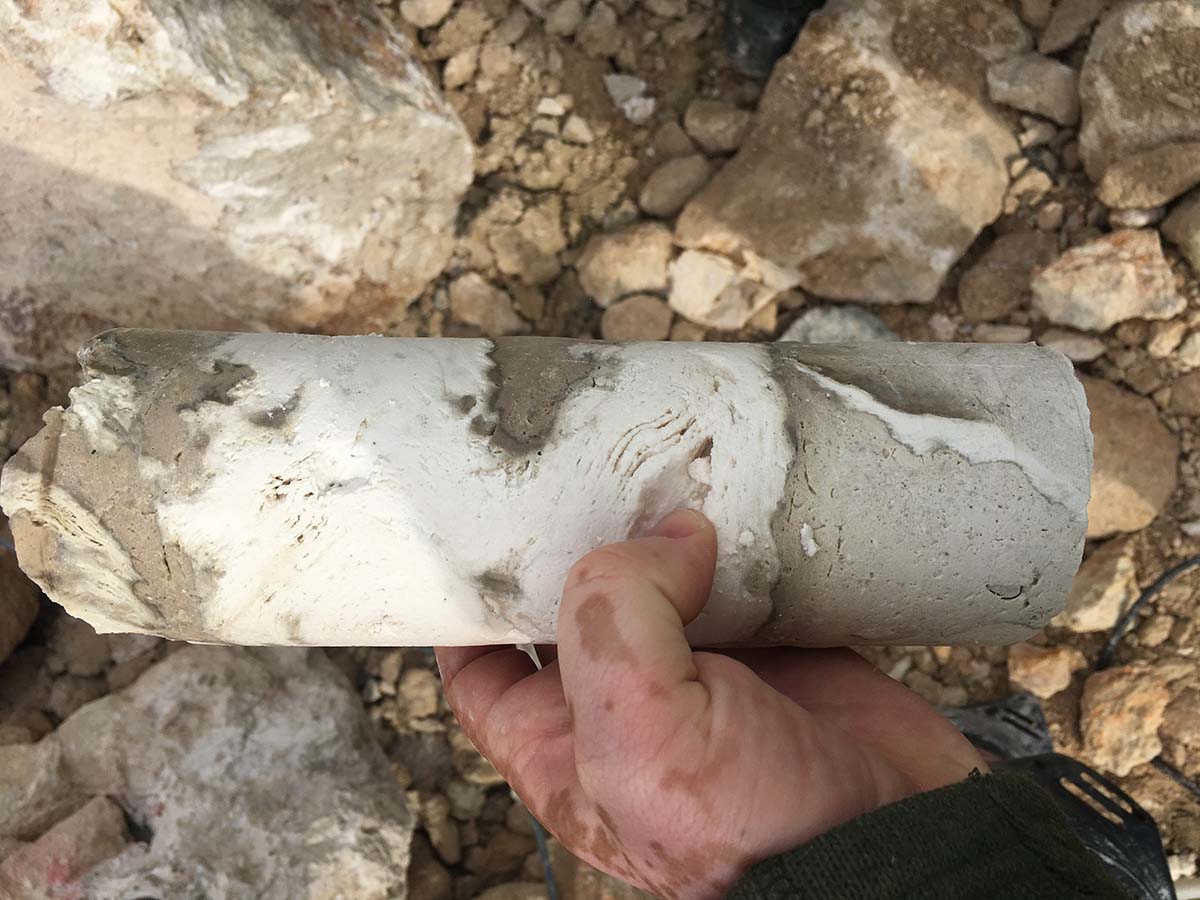
There are a few key things to consider when evaluating stone quality. First, shape matters. Stones should generally be blocky rather than flat or elongated. Bananas, or stones that have sides that exceed roughly three units wide to one unit high, are a definite no-no. This proportion makes it difficult to achieve interlock with other armor stones, makes them more likely to be displaced by waves or ice, and makes them prone to being cracked by the weight of other stones in the final assembly.
Second, stone must be carefully inspected for cracks or weak points. Even hairline cracks or veins in the material can be areas of weakness and make the stone more prone to cracking as it goes through the wetting and drying cycle, is exposed to saltwater, or is hit by crushing ice. If you know what you’re listening for, a hammer can be used to accompany visual inspection. A hammer hitting a quality stone sounds like a thud rather than a hollow sound. For a slightly more dramatic method, a drop test can be performed. The stone is lifted about 12-15 feet off the ground and dropped onto a hard surface. Stones that break when tested, show visual or auditory signs of cracking, or are incorrectly proportioned should be all rejected as armor stone.
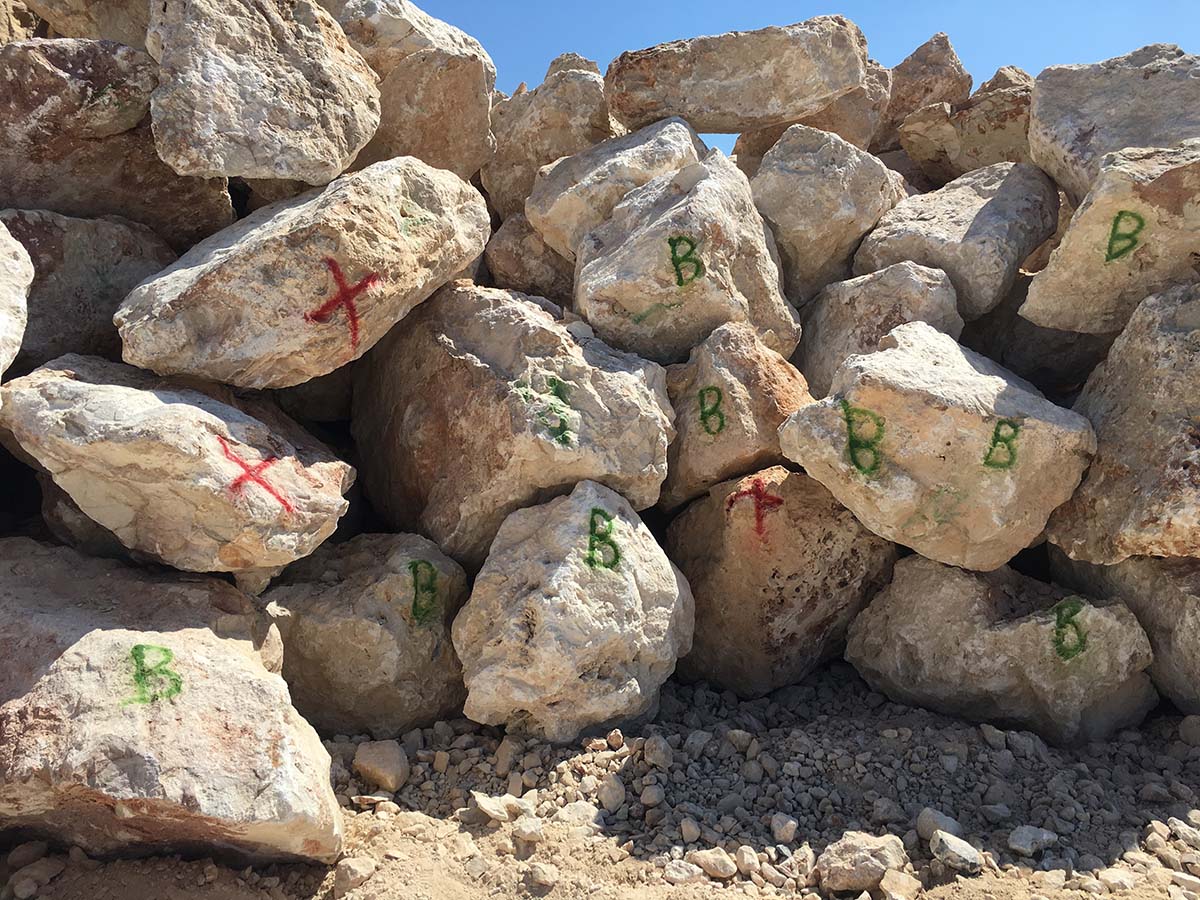
In some cases, if a material fractures into smaller size stone, it may be perfectly suitable to use (or reuse) for some other application – potentially on the interior layers of a breakwater or revetment. This applies not only to newly quarried stone but also to reusing older stone that is already in place and has been exposed to water for a long time. The issue of stone age came up recently on a SmithGroup project with 40-year-old armor stone installed along a shoreline in Lake Michigan. What initially appeared suitable for reuse as armor stone on a shoreline modification project ended up being riddled with small fissures; when the stone was handled with excavation equipment it crumbled apart. After further evaluation, it was determined that the resulting smaller stone material would be suitable for reuse within the improved revetment structure, with new filter and armor stone placed on top of it.
Look to the Source
Inspections and assessments of the material itself only tell part of the story. A fuller understanding of quality requires starting at the beginning of the stone production process with a visit to the quarry. This visit helps answer several critical questions – including “Does the quarry have an adequate supply of the type and size stone needed for the project?” Running out of stone midway through a marine construction project can be devastating, leaving the partially completed structures exposed to damage and prone to washing away.
Other questions that can be cleared up by a quarry inspection include:
• What is the production rate?
• Will their approach to blasting and removal result in the size of material needed without producing detrimental cracks?
• Is there documentation that helps certify their stone meets exacting marine-quality specifications, and does that cover the general type of stone being produced there or only stone from a specific segment of the quarry?
Getting a representative sample of stone from the quarry for additional testing is extremely important, particularly since visual inspection alone can’t discern all the desired characteristics. Determining a stone’s specific gravity, or density, is critical, since less dense stone may shift too easily while too dense stone may result in purchasing a much higher tonnage of material than is needed for a coastal structure. How much water will the stone absorb and what is its ability to withstand repeated wetting and drying? Are there geological inclusions in the stone that make the stone more susceptible to degradation from saltwater? There are tests for all these things. Accounting for the variability of quarried stone can be the difference between a structure that crumbles in a couple of years after placement or lasts its desired life, of 50 or 100 years long.
Set Yourself Up for Construction Success
Stone testing and inspection are only half the battle. Moving a quality material from the quarry to an on-site stockpile location and then placing it correctly are key to successful construction. Thankfully, there are some guiding strategies that can make these steps more efficient and effective.
At the quarry – Create a visual guide for quarry production staff. Label a representative sample of each type and class of stone needed for the project and organize material into separate piles. This makes sorting the stone more efficient for crews while also simplifying it for those in charge of inspecting and testing the stone. Visual sorting using sample stones is not an exact science, as a difference of only three inches in the diameter of a stone can add an entire ton to its weight. To verify before the material is hauled to a site, large ston
e can be loaded onto a truck and weighed. You can divide the overall weight of the load by the number of stones to confirm that the average stone size specified for the job is being met or exceeded.
On the job site – Unload the stone into piles that mirror the distinct classifications established at the quarry. Review the stone, setting aside those broken or cracked as part of the transport and unloading process. Those inspecting the stone on behalf of the owner will appreciate the organization as this makes it much simpler to review.
During construction – Place the stone while continuing to identify and set aside stones that have been damaged during the moving or installation process and won’t perform properly. The best time to reject a stone is before it’s been placed. Reviewing and rejecting already placed stone is very difficult for owners or owner’s representatives due to stone overlap. And for contractors and owners, the need to rework segments of stone structures once they are partially constructed due to the inclusion of bananas or poor stone is extremely costly in both time and money.
Stone is likely to remain in high demand as a critical design material for shoreline protection and marina projects globally. Making sure you are purchasing and using the right quality of stone for the job is ultimately the best and most cost-effective way to safeguard your investment – and to build a facility to last.
Jason Stangland is waterfront practice director for SmithGroup. He can be contacted at jason.stangland@smithgroup.com
Categories | |
Tags |